- are designed in accordance with a modular concept and are highly versatile in application ➤ section
- are suitable for different bearing types and sizes with bore diameters from 20 mm to 160 mm ➤ section
- can be combined with an extensive range of seals covering a wide range of requirements and temperatures ➤ Figure and ➤ section
Seals for split plummer block housings SNV
T = permissible long term temperature of seal
|
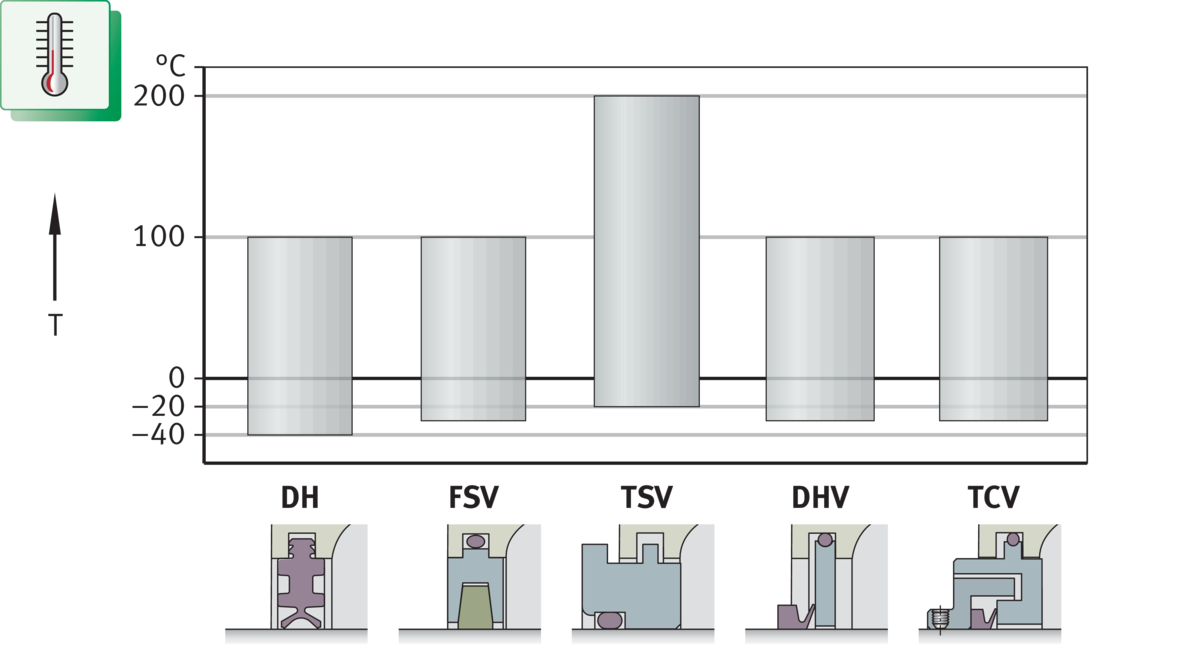 |
Housings for wide range of applications
Split plummer block housings SNV and the associated bearings form bearing arrangement units that can be matched, through the appropriate selection of accessories, to a wide range of applications ➤ Figure. Applications include agricultural machinery, the paper processing industry, mining, materials processing, the steel industry and power stations.
Split plummer block housing SNV
Housings SNV052 to SNV200 are supplied without an eye bolt, housings SNV215 to SNV340 are supplied with an eye bolt
|
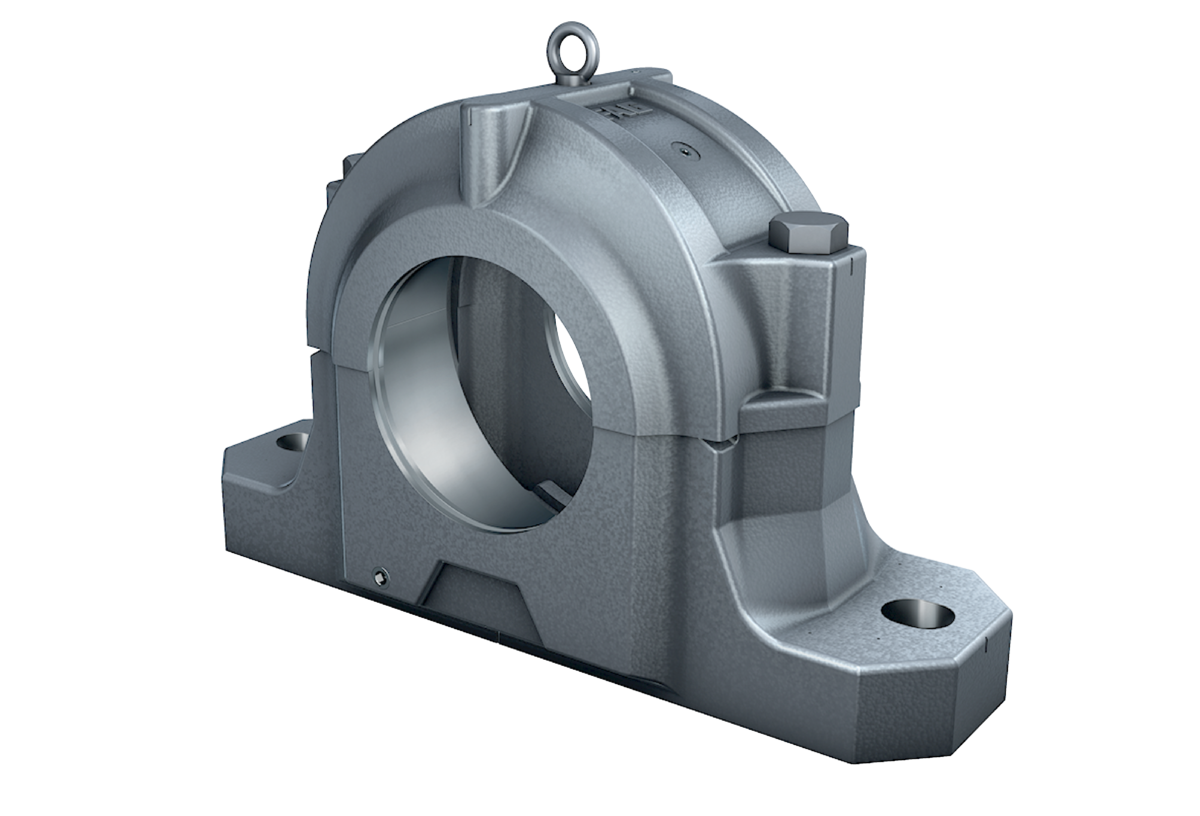 |
Modular concept
The decisive factor is the outside diameter of the bearing
The housings are designed in accordance with a modular concept. Each housing can be fitted with rolling bearings of various diameter and width series if they have the correct outside diameter for the housing.
Seals are matched to the shaft diameter
Depending on their design, the bearings can be located either directly on the shaft or by means of an adapter sleeve. This gives different shaft diameters for the same bearing size. The spacings between the shaft and housing body are compensated by means of appropriately matched seals.
Shaft diameters from 20 mm to 160 mm and from 3/4 inch to 5 1/2 inch
Split plummer block housings SNV are intended for fitting with spherical roller bearings, toroidal roller bearings, self-aligning ball bearings and barrel roller bearings with a tapered or cylindrical bore as well as deep groove ball bearings ➤ Table. The range of shaft diameters is 20 mm to 160 mm and 3/4 inch to 5 1/2 inch.
Bearing types and sizes
Bearing type
|
Size
|
Spherical roller bearings |
- with tapered bore and adapter sleeve
|
21307..-K to 21322..-K
|
- with tapered bore and adapter sleeve
|
22205..-K to 22232..-K
|
- with tapered bore and adapter sleeve
|
22308..-K to 22332..-K
|
- with tapered bore and adapter sleeve
|
23218..-K to 23232..-K
|
|
21304 to 21322
|
|
22205 to 22232
|
|
22308 to 22332
|
|
23218 to 23232
|
Toroidal roller bearings |
- with tapered bore and adapter sleeve
|
C2212..-K to C2232..-K
|
- with tapered bore and adapter sleeve
|
C2312..-K to C2332..-K
|
- with tapered bore and adapter sleeve
|
C3218..-K to C3232..-K
|
|
C2212 to C2232
|
|
C2312 to C2332
|
|
C3218 to C3232
|
continued ▼
|
Bearing types and sizes
Bearing type
|
Size
|
Self-aligning ball bearings |
- with tapered bore and adapter sleeve
|
1205-K to 1222-K
|
- with tapered bore and adapter sleeve
|
1305-K to 1320-K
|
- with tapered bore and adapter sleeve
|
2205-K to 2220-K
|
- with tapered bore and adapter sleeve
|
2305-K to 2320-K
|
|
1205 to 1222
|
|
1305 to 1320
|
|
2205 to 2220
|
|
2304 to 2320
|
Barrel roller bearings |
- with tapered bore and adapter sleeve
|
20205-K to 20232-K
|
- with tapered bore and adapter sleeve
|
20305-K to 20332-K
|
|
20205 to 20232
|
|
20305 to 20330
|
Deep groove ball bearings |
|
|
6205 to 6232
|
|
6304 to 6332
|
continued ▲
|
Split spherical roller bearings
Unsplit spherical roller bearings with an adapter sleeve can be replaced by split spherical roller bearings. This gives a considerable reduction in the work associated with bearing replacement in numerous applications.
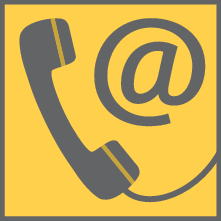
In order to ensure selection of the correct combination of housing and bearing when using split bearings, please contact Schaeffler.
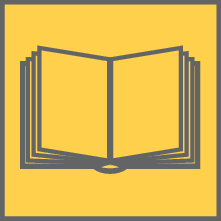
The range of split spherical roller bearings is described in detail in a separate publication TPI 250.
Materials
The standard material for the housing bodies is flake graphite cast iron EN‑GJL-HB215 in accordance with DIN EN 1561 (suffix L). By agreement, housing bodies made from spheroidal graphite cast iron EN-GJS-400-15 in accordance with DIN EN 1563 (suffix D) are available.
Corrosion protection
All outer surfaces not machined by chip-forming methods have a universal paint coating (colour RAL 7031, blue grey). The coating can be finished using all synthetic resin, polyurethane, acrylic, epoxy resin, chlorinated rubber, nitrocellulose and acid-hardening hammer tone finishes.
Inner and outer surfaces machined by chip-forming methods are provided with anti-corrosion protection that can be easily removed. It is recommended that only volatile solvents and lint-free cloths should be used.
Locating bearing arrangement by means of locating rings
The bearing seats in the housing are machined such that the bearings are movable in the housing and can thus function as non-locating bearings. Locating bearing arrangements can be achieved by the insertion of one locating ring FRM on each side of the bearing outer ring. The bearing is thus seated in the centre of the housing. Locating rings must be ordered separately.
Guide values
Guide values are given for the rupture load of plummer block housings SNV and the maximum load carrying capacity of connecting screws for the upper and lower housing sections ➤ Figure and ➤ Table. The guide values are valid for purely static loading.
The guide values for housing rupture load are valid for the standard housing material flake graphite cast iron (suffix L). For spheroidal graphite cast iron (suffix D) a factor of 1,6 should be applied.
The guide values only apply if the flatness of the mounting surface in accordance with DIN EN ISO 1101 corresponds to the tolerance grade IT8 in accordance with DIN EN ISO 286-1 (measured across the diagonal). A precondition for supporting loads is that the housing base surface is completely and rigidly supported.
Safety factors
When determining the permissible static load, safety factors must be applied:
- safety factor of 6 relative to the housing rupture load
- safety factor of 3 relative to the maximum load carrying capacity of the connecting screws
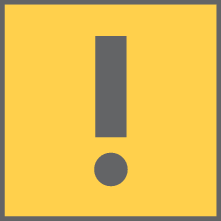
The housing must not be subjected to an axial load of more than 2/3 of the housing rupture load F180°.
If the housing is subjected to axial load, the permissible axial load of the bearing fitted must be taken into consideration. If the bearing is located on the shaft using an adapter sleeve, the axial retaining force of the bearing and adapter sleeve must also be taken into consideration.
If the load direction is between 55° and 120° or axial load is present, we recommend that the housings should be secured in the load direction by means of stops or dowels.
Load directions F for the guide values for the housing rupture load and the maximum load carrying capacity of the connecting screws
|
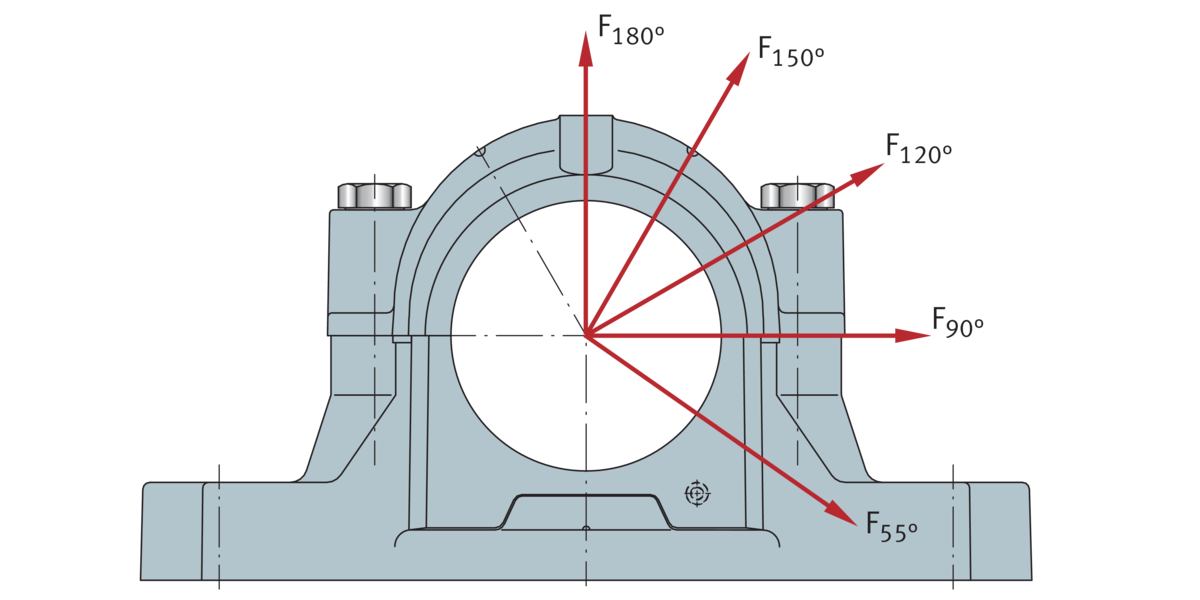 |
Guide values for housing rupture load and maximum load carrying capacity of connecting screws. Tightening torques
Housing
|
Housing rupture load in load direction F Housing made from flake graphite cast iron
|
Connecting screws
|
Designation
|
|
Thread to DIN 13
|
Tightening torque1)
|
Maximum load carrying capacity in load direction F2)
|
|
55°
|
90°
|
120°
|
150°
|
180°
|
Grade 8.8
|
|
120°
|
150°
|
180°
|
|
kN
|
kN
|
kN
|
kN
|
kN
|
Nm
|
kN
|
kN
|
kN
|
SNV052-F-L
|
160
|
95
|
70
|
60
|
80
|
M10
|
51
|
60
|
35
|
30
|
SNV062-F-L
|
170
|
100
|
80
|
65
|
85
|
M10
|
51
|
60
|
35
|
30
|
SNV072-F-L
|
190
|
110
|
85
|
80
|
95
|
M10
|
51
|
60
|
35
|
30
|
SNV080-F-L
|
210
|
130
|
95
|
85
|
105
|
M10
|
51
|
60
|
35
|
30
|
SNV085-F-L
|
225
|
140
|
100
|
90
|
120
|
M10
|
51
|
60
|
35
|
30
|
SNV090-F-L
|
265
|
160
|
120
|
105
|
130
|
M10
|
51
|
60
|
35
|
30
|
SNV100-F-L
|
280
|
170
|
125
|
120
|
140
|
M12
|
87
|
80
|
45
|
40
|
SNV110-F-L
|
300
|
180
|
130
|
125
|
150
|
M12
|
87
|
80
|
45
|
40
|
SNV120-F-L
|
335
|
200
|
150
|
130
|
170
|
M12
|
87
|
80
|
45
|
40
|
SNV125-F-L
|
335
|
200
|
150
|
130
|
170
|
M12
|
87
|
80
|
45
|
40
|
SNV130-F-L
|
400
|
250
|
180
|
150
|
200
|
M12
|
87
|
80
|
45
|
40
|
SNV140-F-L
|
425
|
265
|
190
|
170
|
210
|
M12
|
87
|
80
|
45
|
40
|
SNV150-F-L
|
475
|
280
|
200
|
180
|
235
|
M12
|
87
|
80
|
45
|
40
|
SNV160-F-L
|
530
|
335
|
250
|
210
|
265
|
M16
|
215
|
180
|
100
|
90
|
SNV170-F-L
|
560
|
355
|
265
|
225
|
280
|
M16
|
215
|
180
|
100
|
90
|
SNV180-F-L
|
630
|
375
|
280
|
250
|
300
|
M20
|
430
|
260
|
150
|
130
|
SNV190-F-L
|
630
|
375
|
280
|
250
|
300
|
M20
|
430
|
260
|
150
|
130
|
SNV200-F-L
|
670
|
400
|
315
|
280
|
335
|
M20
|
430
|
260
|
150
|
130
|
SNV215-F-L
|
800
|
450
|
355
|
315
|
400
|
M20
|
430
|
260
|
150
|
130
|
SNV230-F-L
|
900
|
530
|
400
|
355
|
450
|
M24
|
740
|
360
|
210
|
180
|
SNV240-F-L
|
1000
|
600
|
450
|
400
|
500
|
M24
|
740
|
360
|
210
|
180
|
SNV250-F-L
|
1060
|
630
|
475
|
425
|
530
|
M24
|
740
|
360
|
210
|
180
|
SNV260-F-L
|
1180
|
710
|
530
|
475
|
600
|
M24
|
740
|
360
|
210
|
180
|
SNV270-F-L
|
1180
|
710
|
530
|
475
|
600
|
M24
|
740
|
360
|
210
|
180
|
SNV280-F-L
|
1320
|
750
|
600
|
530
|
630
|
M24
|
740
|
360
|
210
|
180
|
SNV290-F-L
|
1400
|
850
|
630
|
560
|
710
|
M24
|
740
|
360
|
210
|
180
|
SNV300-F-L
|
1500
|
900
|
670
|
600
|
750
|
M24
|
740
|
360
|
210
|
180
|
SNV320-F-L
|
1700
|
1000
|
750
|
670
|
850
|
M24
|
740
|
360
|
210
|
180
|
SNV340-F-L
|
1900
|
1120
|
850
|
750
|
950
|
M30
|
1450
|
640
|
370
|
320
|
- The tightening torques are maximum values when utilising 90% of the yield stress of the screw material and with a friction factor of 0,14. We recommend that the screws should be inserted to 70% of these values.
- Maximum load carrying capacity in load direction F, where there is still contact at the parting line between the upper and lower housing sections.
Housings made from spheroidal graphite cast iron (suffix D) have a housing rupture load that is 1,6 times higher than that of housings made from flake graphite cast iron.
Grease lubrication
Split plummer block housings SNV are principally intended for grease lubrication. The housings can, however, also be supplied in a design for oil lubrication.
Lubricating greases
Suitable greases
Arcanol MULTITOP, a lithium soap grease of NLGI class 2 with particularly effective EP additives, is highly suitable under the following conditions:
- bearing operating temperatures < +100 °C
- bearing loads P/C < 0,3
- bearing-specific speed parameter kf · n · dM < 700 000 min–1 · mm where: kf = 1 for self-aligning ball bearings and deep groove ball bearings, kf = 8 to 10,5 for spherical roller bearings
Due to their favourable flow behaviour, greases of NLGI grade 2, such as Arcanol MULTITOP and Arcanol MULTI2, are more suitable for relubrication than greases of higher consistency grades.
Grease quantities
Basic rule for initial greasing
For initial greasing, the basic rule is that the bearing should be filled with grease to 100% and the free volume of the housing to 60%. This is the basis for the recommended grease quantities ➤ Table. The free volume is the space that remains in the housing once the bearing, adapter sleeve, shaft and seals have been fitted.
Relubrication
For relubrication, minimum quantities of grease are recommended ➤ Table.
Recommended grease quantities for initial greasing and relubrication
Housing
|
Grease quantity
|
Initial greasing
|
Relubrication (minimum quantity)
|
≈ g
|
≈ g
|
SNV052-F
|
30
|
5
|
SNV062-F
|
45
|
5
|
SNV072-F
|
65
|
10
|
SNV080-F
|
80
|
10
|
SNV085-F
|
105
|
10
|
SNV090-F
|
130
|
10
|
SNV100-F
|
180
|
15
|
SNV110-F
|
210
|
15
|
SNV120-F
|
270
|
20
|
SNV125-F
|
290
|
20
|
SNV130-F
|
330
|
20
|
SNV140-F
|
440
|
25
|
SNV150-F
|
500
|
30
|
SNV160-F
|
650
|
40
|
SNV170-F
|
700
|
45
|
SNV180-F
|
900
|
55
|
SNV190-F
|
950
|
60
|
SNV200-F
|
1 200
|
70
|
SNV215-F
|
1 400
|
80
|
SNV230-F
|
1 600
|
85
|
SNV240-F
|
1 700
|
90
|
SNV250-F
|
2 000
|
100
|
SNV260-F
|
2 000
|
120
|
SNV270-F
|
2 500
|
130
|
continued ▼
|
Recommended grease quantities for initial greasing and relubrication
Housing
|
Grease quantity
|
Initial greasing
|
Relubrication (minimum quantity)
|
≈ g
|
≈ g
|
SNV280-F
|
2 600
|
140
|
SNV290-F
|
3 000
|
150
|
SNV300-F
|
3 100
|
160
|
SNV320-F
|
3 700
|
200
|
SNV340-F
|
4 500
|
240
|
continued ▲
|
Special case with 100% grease filling
With a speed parameter n · dM < 50 000 min–1 · mm and a non-contact seal (labyrinth seal TSV), where the grease should also perform a sealing function, the housing and seal cavities should be filled to 100%.
Relubrication
Bearings with circumferential lubrication groove
Where relubrication is carried out on bearings with a circumferential lubrication groove, the grease is introduced into the housing via the central lubrication hole ➤ Figure. In this type of relubrication, the grease acts directly on the bearing raceway.
Bearings without lubrication groove
Where relubrication is carried out on bearings without a lubrication groove, the grease must be introduced into the housing via the lateral lubrication hole. In this case, the housing cavities on the side with the lubrication nipple must be filled completely with grease so that the relubrication grease can act immediately on the bearing.
Permanent use of lubrication nipples
In both cases, the lubrication hole present (threaded hole M10×1) is prepared by removing the screw plug and permanently inserting one of the lubrication nipples supplied at this point.
Marked positions for further lubrication holes
As an alternative to the lubrication holes already present, lubrication holes may be introduced at other positions as indicated by the cast-in marking points.
Lubrication holes can be introduced at further marked positions for the relubrication of labyrinth seals.
Prevention of overgreasing
For relubrication, minimum quantities of grease are recommended ➤ Table. In order to prevent overgreasing, the screw plug in the grease outlet hole in the lower housing section must be removed while relubrication is being carried out. This allows superfluous grease to escape. This must be observed in particular when using double lip seals DH. Otherwise, there is a risk that the double lip seal will be pressed out of the housing.
The grease outlet hole must then be closed off again using the screw plug.
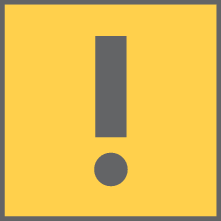
If unfavourable environmental conditions are present, there is therefore a risk of contaminant ingress into the housing when the grease outlet holes are opened.
Positions for relubrication
 SNV052-F to SNV200-F
 SNV215-F to SNV340-F
 Central lubrication hole, for bearings with lubrication groove
 Lateral lubrication hole, for bearings without lubrication groove
 Marked positions for further lubrication holes for lubrication of the bearing
 Marked positions for further lubrication holes for lubrication of seals
 Grease outlet hole
|
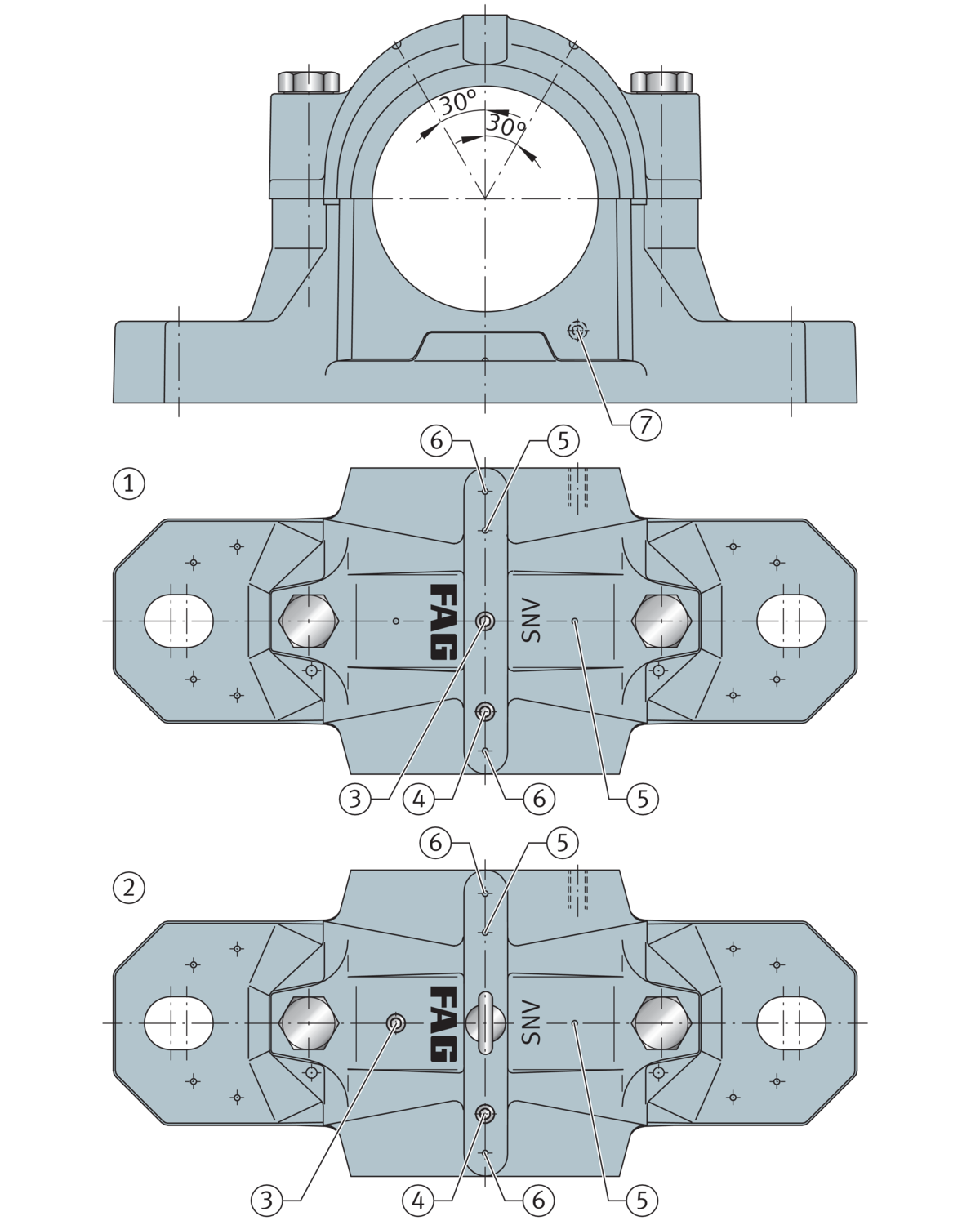 |
Standard parts and dimensions
Screw plugs
The lubrication and grease outlet holes are closed off using screw plugs to DIN 906.
Lubrication nipples
Lubrication nipples with a dust cap are supplied as followed:
- button head lubrication nipples to DIN 3404-M10×1
- taper type lubrication nipple to DIN 71412-AM10×1
Dimensions
The size of the grease outlet hole is dependent on the size of the housing ➤ Table.
Dimensions of threaded holes
Housing
|
Thread for
|
Grease outlet hole
|
Relubrication hole
|
SNV052-F – SNV090-F
|
M10×1
|
M10×1
|
SNV100-F – SNV125-F
|
M14×1,5
|
M10×1 |
SNV130-F – SNV340-F
|
M20×1,5
|
M10×1 |
Oil lubrication
Suitability for oil bath and recirculating oil lubrication
Split plummer block housings SNV are suitable not only for grease lubrication but also for oil bath lubrication and recirculating oil lubrication. The housings have a large internal cavity with oil collector pockets in the lower section. Due to the housing geometry, it is possible to introduce connection holes for oil inlet, oil outlet, an oil sight glass and a temperature sensor.
Connection holes for oil lubrication
Dimensions
The recommended dimensions are valid for oil bath lubrication and for recirculating oil lubrication ➤ Table, ➤ Table and ➤ Figure.
Utilisation
If recirculating oil lubrication is used, the hole M2 is intended for the oil inlet function. If oil bath lubrication is used, a venting device can be installed for venting of the housing.
If oil bath lubrication is used, the hole M4 is intended for the oil sight glass. If recirculating oil lubrication is used, the hole can be used for the oil outlet.
Recommended dimensions of connnection holes for oil inlet and oil outlet
Housing
|
Connection for
|
Oil inlet
|
Oil outlet
|
M2
|
n3/2
|
M3
|
α
|
g6
|
mm
|
°
|
mm
|
SNV100-F
|
G1/4
|
31
|
M10×1
|
50
|
44
|
SNV110-F
|
G1/4 |
33,5
|
M10×1
|
50
|
46
|
SNV120-F
|
G1/4 |
35,5
|
M10×1
|
50
|
49
|
SNV125-F
|
G1/4 |
28,5
|
M10×1
|
50
|
49
|
SNV130-F
|
G1/4 |
38
|
M10×1
|
50
|
51,5
|
SNV140-F
|
G1/4 |
40,5
|
M10×1
|
60
|
57,5
|
SNV150-F
|
G1/4 |
42,5
|
M10×1
|
60
|
60
|
SNV160-F
|
G1/4 |
45
|
M10×1
|
60
|
62,5
|
SNV170-F
|
G1/4 |
46,5
|
M10×1
|
60
|
64
|
SNV180-F
|
G1/4 |
19,5
|
M10×1
|
60
|
69
|
SNV190-F
|
G1/4 |
49,5
|
M10×1
|
60
|
68,5
|
SNV200-F
|
G1/4 |
55,5
|
M10×1
|
60
|
77,5
|
SNV215-F
|
G1/4 |
58,5
|
M10×1
|
60
|
80
|
SNV230-F
|
G1/4 |
61
|
M10×1
|
60
|
83
|
SNV240-F
|
G1/4 |
60
|
M10×1
|
60
|
81,5
|
SNV250-F
|
G1/4 |
65,5
|
M10×1
|
60
|
89
|
SNV260-F
|
G1/4 |
62,5
|
M10×1
|
60
|
84
|
SNV270-F
|
G1/4 |
71,5
|
M10×1
|
60
|
86,5
|
SNV280-F
|
G1/4 |
68
|
M10×1
|
60
|
92,5
|
SNV290-F
|
G1/4 |
76
|
M10×1
|
60
|
102,5
|
SNV300-F
|
G1/4 |
73
|
M10×1
|
60
|
99,5
|
SNV320-F
|
G1/4 |
77
|
M10×1
|
60
|
105,5
|
SNV340-F
|
G1/4 |
81
|
M10×1
|
60
|
109,5
|
Recommended dimensions of connection holes for oil sight glass
Housing
|
Connection for oil sight glass
|
M4
|
g7
|
h3
|
D5
|
mm
|
SNV100-F
|
G3/8
|
33
|
31
|
24
|
SNV110-F
|
G3/8 |
35
|
28
|
24
|
SNV120-F
|
G3/8 |
38
|
35
|
24
|
SNV125-F
|
G3/8 |
44
|
24
|
24
|
SNV130-F
|
G1/2
|
43
|
28,5
|
30
|
SNV140-F
|
G1/2 |
45
|
40
|
30
|
SNV150-F
|
G1/2 |
47
|
38
|
30
|
SNV160-F
|
G1/2 |
50
|
39
|
30
|
SNV170-F
|
G3/4 |
55
|
46
|
36
|
SNV180-F
|
G3/4 |
57
|
43
|
36
|
SNV190-F
|
G3/4 |
48
|
45
|
36
|
SNV200-F
|
G3/4 |
62
|
50
|
36
|
SNV215-F
|
G3/4 |
67
|
58
|
36
|
SNV230-F
|
G3/4 |
70
|
60
|
36
|
SNV240-F
|
G3/4 |
61
|
60
|
36
|
SNV250-F
|
G3/4 |
75
|
55
|
36
|
SNV260-F
|
G3/4 |
65
|
65
|
36
|
SNV270-F
|
G3/4 |
81
|
55
|
36
|
SNV280-F
|
G3/4 |
70
|
60
|
36
|
SNV290-F
|
G3/4 |
87
|
58
|
36
|
SNV300-F
|
G3/4 |
75
|
70
|
36
|
SNV320-F
|
G3/4 |
80
|
73
|
36
|
SNV340-F
|
G3/4 |
95
|
75
|
36
|
Dimensions of connection holes
 Venting device
 Screw plug
 Oil sight glass
|
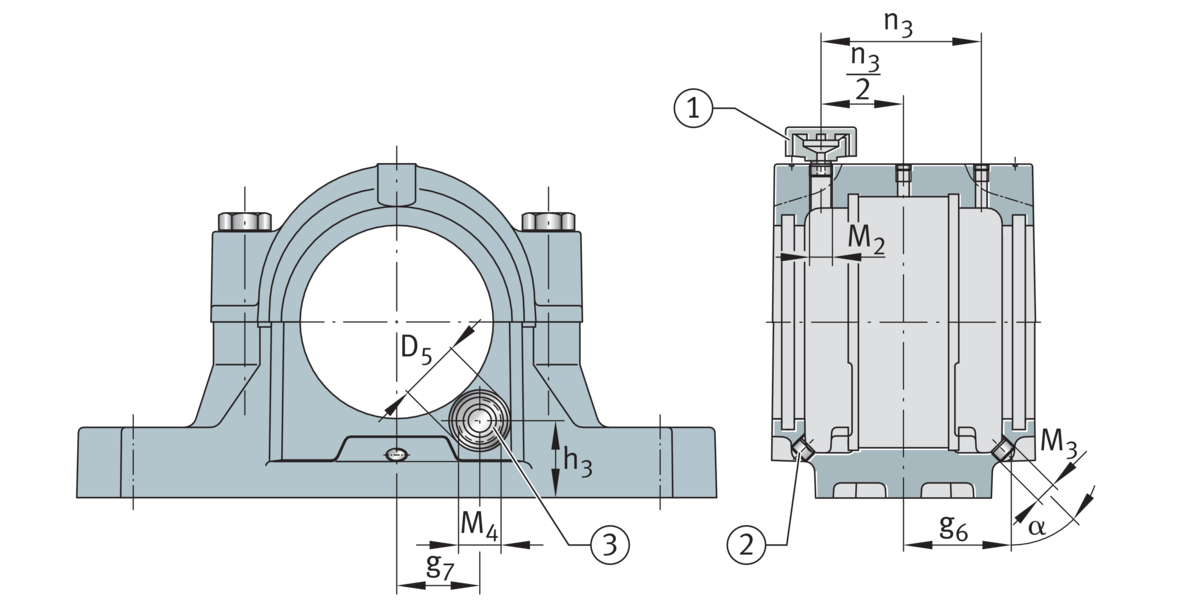 |
Design for oil lubrication
Housings with connection holes for oil lubrication
Plummer block housings SNV can be supplied by agreement in a design for oil lubrication. Housings of this design already have the connection holes for oil inlet, oil outlet and an oil sight glass to the recommended dimensions ➤ Table, ➤ Table and ➤ Figure.
The scope of delivery of the design for oil lubrication includes:
- 1 oil sight glass OSGL
- 1 venting device VENT
- 2 screw plugs VSB
Housings with connection holes according to individual customer specifications can also be supplied once their feasibility has been checked.
Sealing
Sealing of the shaft
When using the double lip seal DH, a certain amount of oil leakage must be expected, which is unavoidable with seals that are split and not spring‑loaded.
In order to limit oil leakage to a small quantity, the shaft in the seal area should have the following characteristics:
- hardness at least 55 HRC
- ground without spiral marks to Ra = 0,2 mm, but at least Ra ≦ 0,5 μm
A technically oiltight design is only possible with a spring-loaded, unsplit rotary shaft seal.
Sealing of the housing body
The parting line between the upper and lower housing sections must be sealed with a thin layer of a commercial sealant (with permanent elasticity). In the case of a housing closed on one side, the base of the groove in which the cover is inserted must be brushed with sealant.
Guidelines for oil bath lubrication
Minimum oil level
When using oil bath lubrication, a minimum oil level must be ensured. This corresponds to the dimension h3 ➤ Table and ➤ Figure.
Housing venting
When using oil bath lubrication, venting of the housing is absolutely necessary.
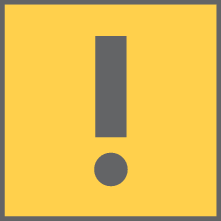
For operation with oil bath lubrication, venting of the housing must be provided. For example, the filling hole can be closed off using a bleed screw.
Seals
Standard seals
For the sealing of the bearing housings, the standard seals available are the double lip seal, the felt seal, the labyrinth seal, the V ring seal and the Taconite seal. These seals are matched to the rectangular section annular slots on both sides of the housings. They are principally suitable for grease lubrication. The seals must be ordered separately. In the case of the double lip seal and felt seal, the scope of delivery comprises two seals, while all other seals are supplied individually. If a continuous shaft is present, two seals must be ordered.
Special seals
Special seals are also available by agreement.
Double lip seal DH
Separate sealing functions inwards and outwards
The seal lips of the double lip seal DH slide on the rotating shaft. The outer seal lip prevents ingress of contamination into the bearing. This effect is supported by the grease inserted between the seal lips. The inner lip prevents lubricant from escaping from the housing. The seal is made from acrylonitrile butadiene rubber NBR and is suitable for circumferential velocities of up to 13 m/s. For continuous operation, a maximum circumferential velocity of 6 m/s is recommended.
The seal is suitable for temperatures from –40 °C to +100 °C. It allows shaft misalignment of up to 0,5° in both directions.
Two-piece seal for simplified fitting
The double lip seal DH is a two-piece seal. It can be easily inserted in the annular slots in the housing. The parting joint of the seal halves should be in the same plane as the parting joint of the housing.
Shaft
The contact running area on the shaft for the seal lips should have a roughness Ra 3,2.
Felt seals FSV
Robust seal for grease lubrication
Felt seals FSV are particularly suitable for grease lubrication. They comprise an adapter holding the inserted, oil-impregnated felt strip and the adapter is secured against rotation by an O ring in the annular slot in the housing. The seals are suitable for circumferential velocities of up to 5 m/s and, after running-in, of up to 15 m/s. They can be used at temperatures up to +100 °C. The permissible shaft misalignment is 0,5° in both directions.
Aramide packing
By agreement, aramide packing is available for temperatures of more than 100 °C.
Labyrinth seals TSV
Non-contact seal for high circumferential velocities
Labyrinth seals TSV give non-contact sealing. They are therefore suitable for high circumferential velocities. The O ring, which is pressed between the labyrinth ring and shaft, is made from fluoro rubber FKM and is suitable for temperatures of up to +200 °C. The labyrinth seal allows shaft misalignment of up to 0,5° in both directions.
Relubrication
If necessary, the labyrinth can be relubricated. For this purpose, a lubrication hole must be made in the upper housing section for each labyrinth seal. The optimum positions are indicated by cast-in pilot holes.
V ring seals DHV
Seal in axial contact
In the case of V ring seals DHV, the seal lip is in axial contact with the sliding surface which is located in the rectangular section annular slot of the housing. The seal is made from NBR and is suitable, when using grease lubrication, for circumferential velocities of up to 12 m/s. If circumferential velocities of more than 8 m/s are present, axial location is necessary. The seal allows shaft misalignment of up to 0,5° in both directions.
Taconite seals TCV
Seal for extreme contamination impact
Taconite seals TCV are combined seals comprising a labyrinth seal and a V ring. These seals are suitable for extreme operating conditions in relation to contamination and dust. The V ring is made from NBR and is suitable for temperatures of up to +100 °C. The Taconite seal allows shaft misalignment of up to 0,5° in both directions.
Covers
Covers are used in the case of housings closed on one side. The covers fit in the rectangular section annular slots in the housings.
Covers DKV
Covers made from plastic
Covers DKV are made from plastic and are suitable for long term temperatures of up to +120 °C. The covers must be ordered separately.
Covers DKVT
Covers made from metal
Covers DKVT are made from steel, flake graphite cast iron or spheroidal graphite cast iron and are suitable for temperatures of up to +200 °C. Covers are available by agreement.
Characteristics and operating limits
The characteristics and operating limits of the standard seals and covers are compared in an overview ➤ Table.
Standard seals and covers for plummer block housings SNV
Seals and covers
++ = highly suitable + = suitable (+) = suitable with restrictions – = not suitable
|
Double lip seal, split
|
Felt seal, split
|
Labyrinth seal, unsplit
|
Seals and covers
++ = highly suitable + = suitable (+) = suitable with restrictions – = not suitable
|
V ring seal, unsplit
|
Taconite seal, unsplit
|
Covers
|
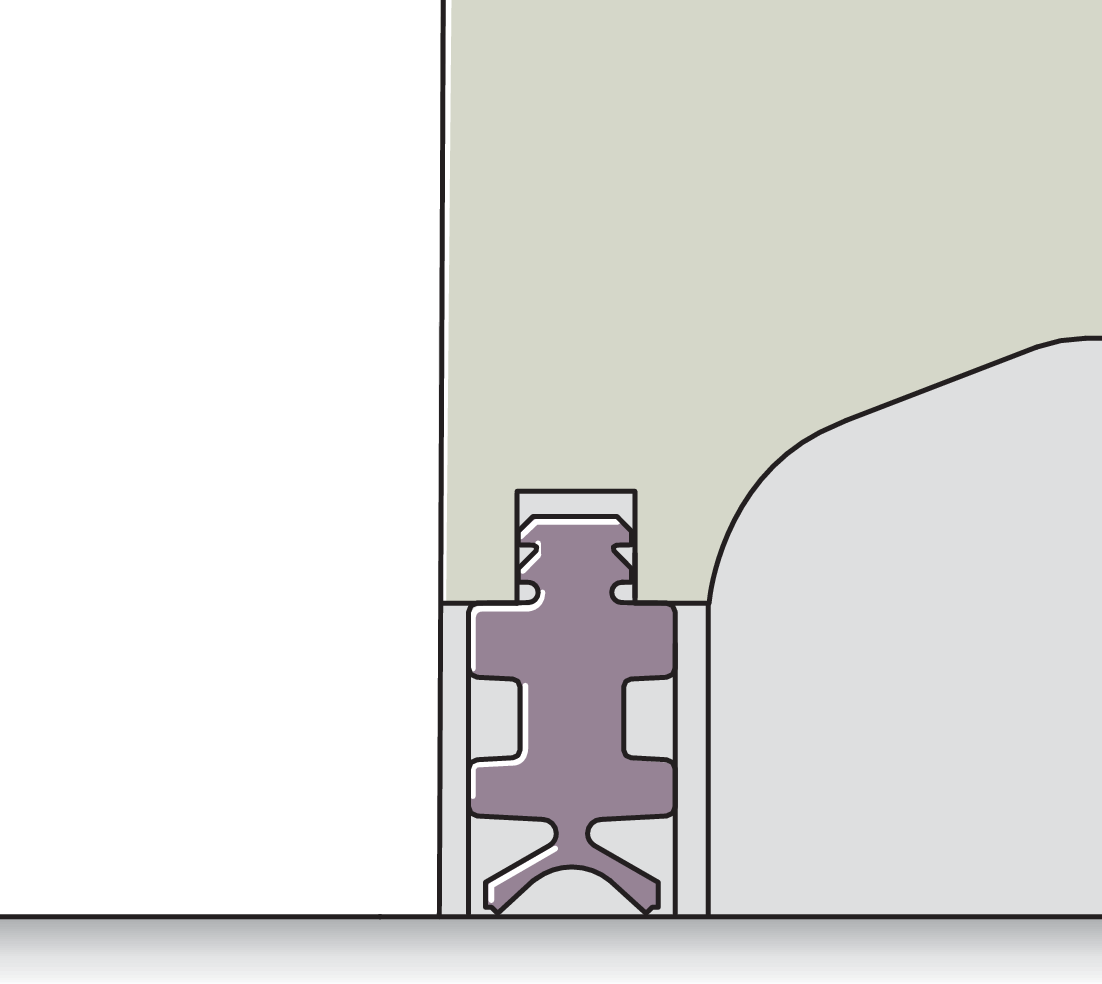 |
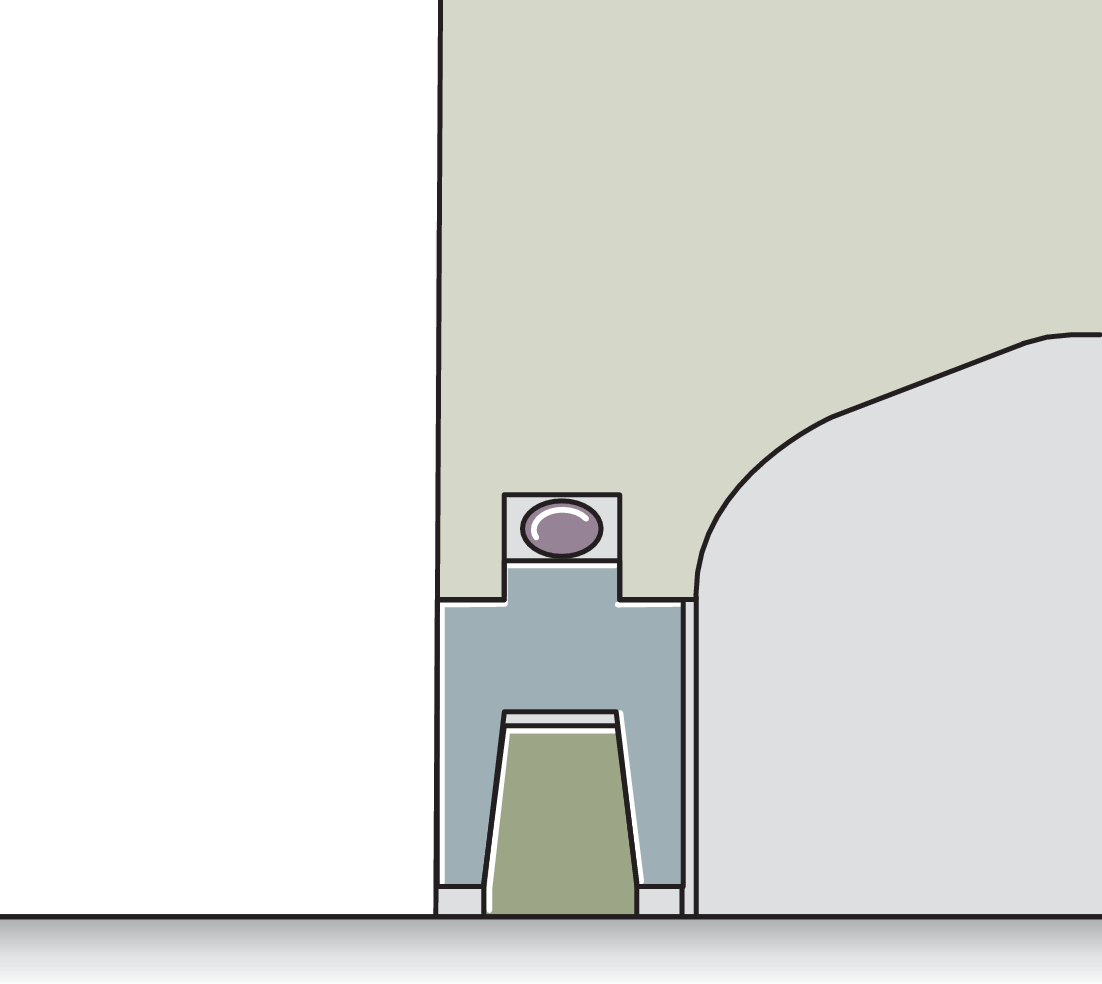 |
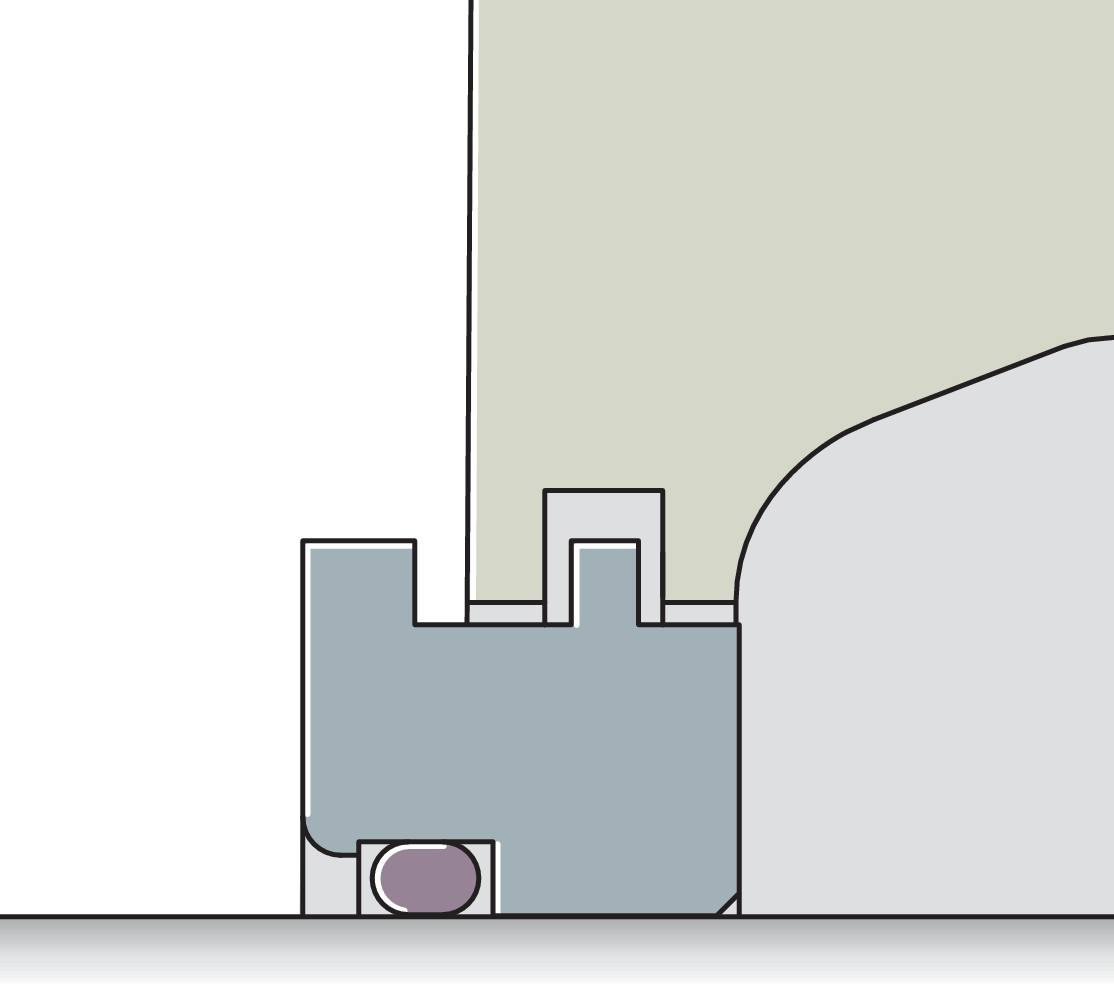 |
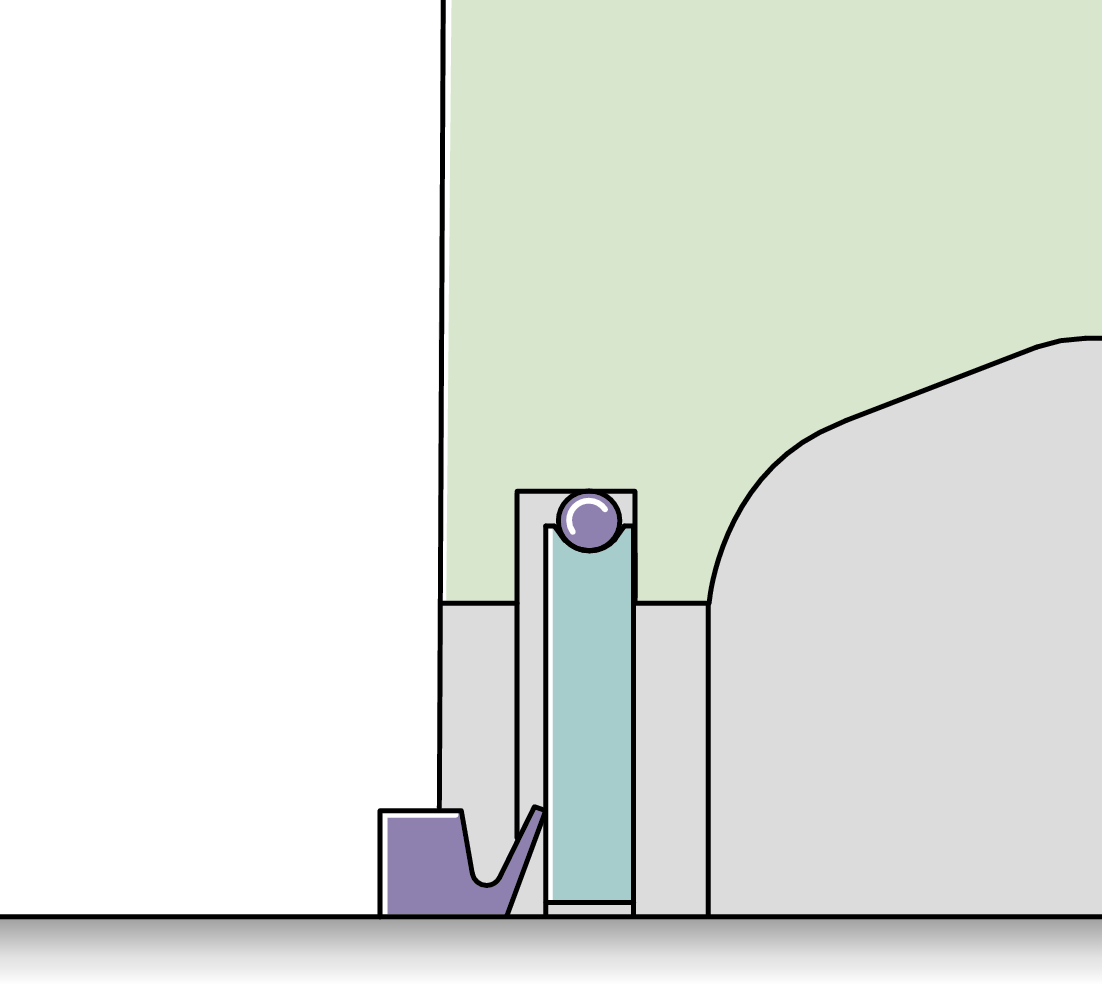 |
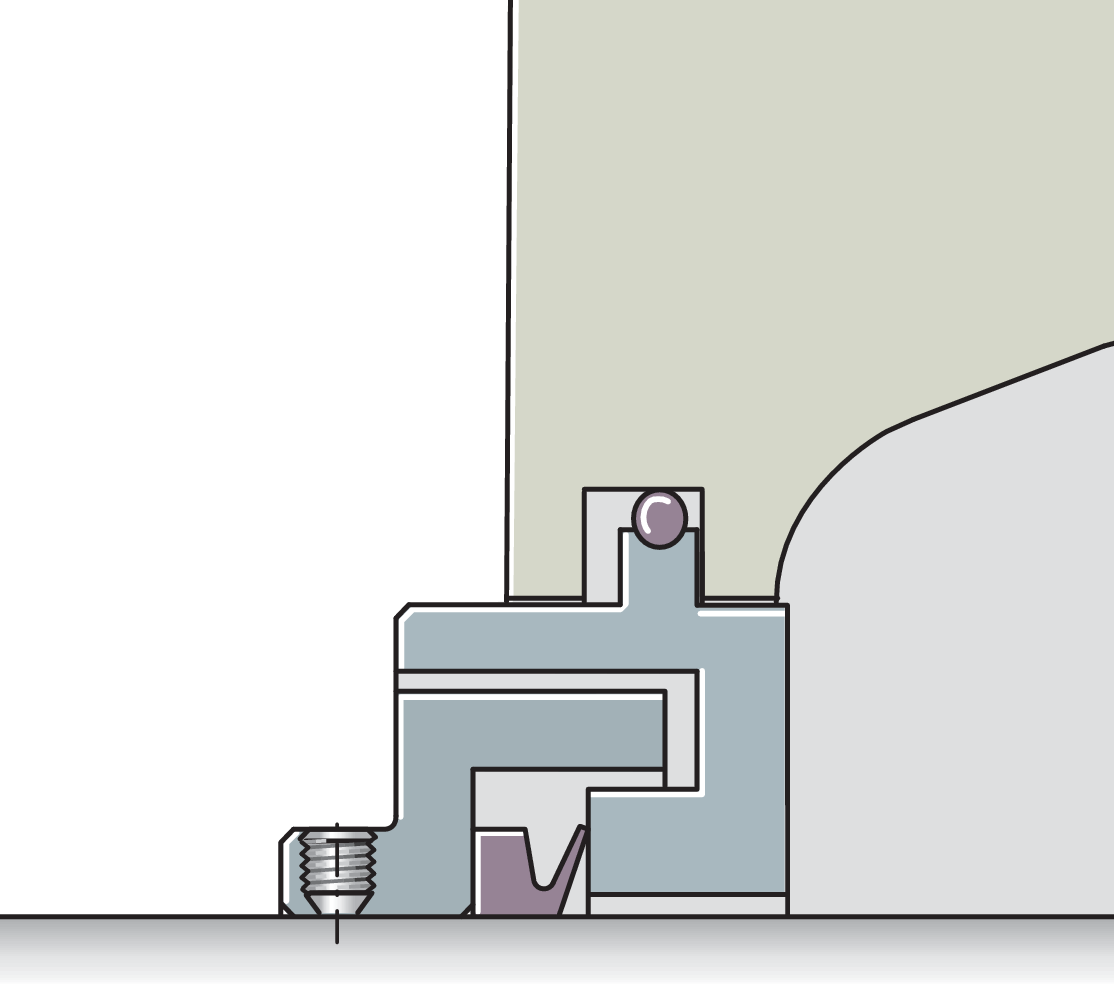 |
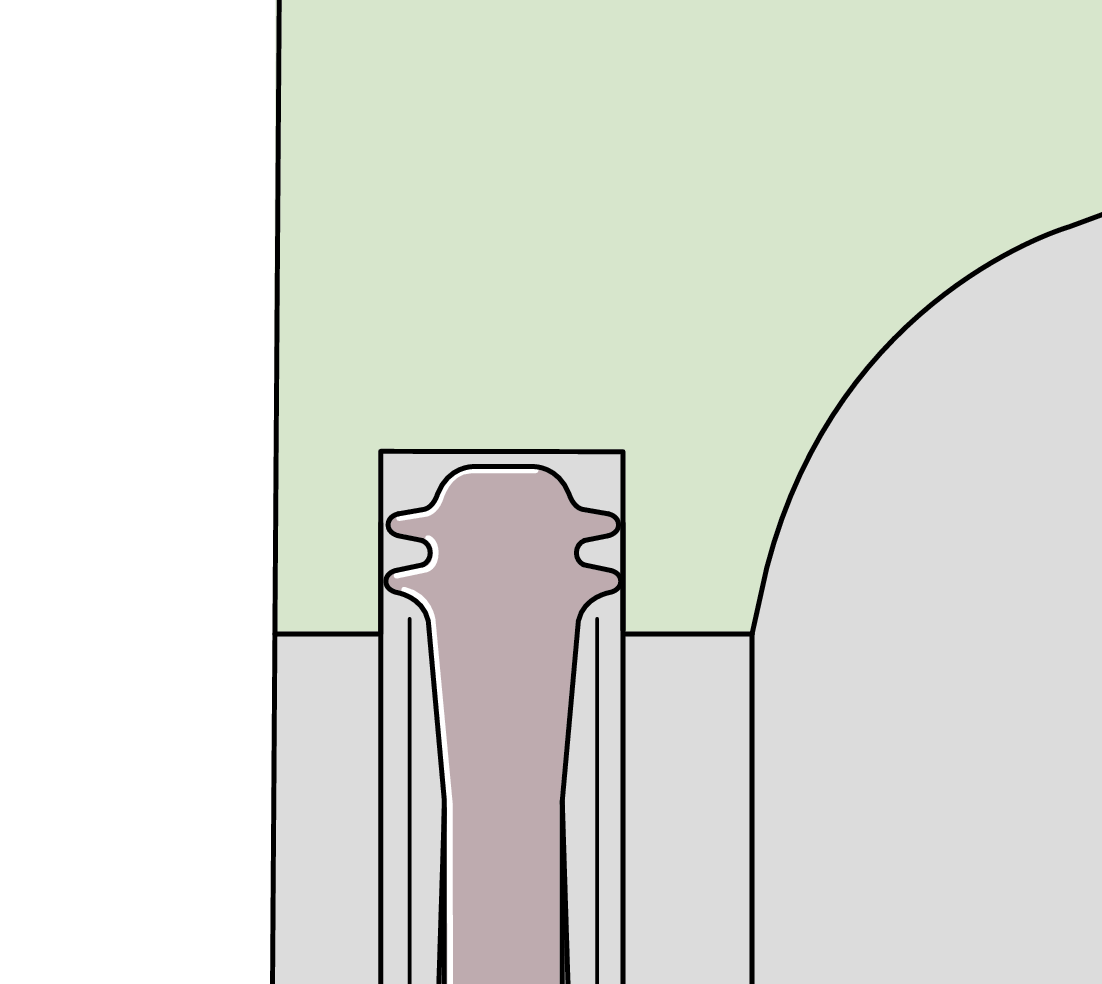 |
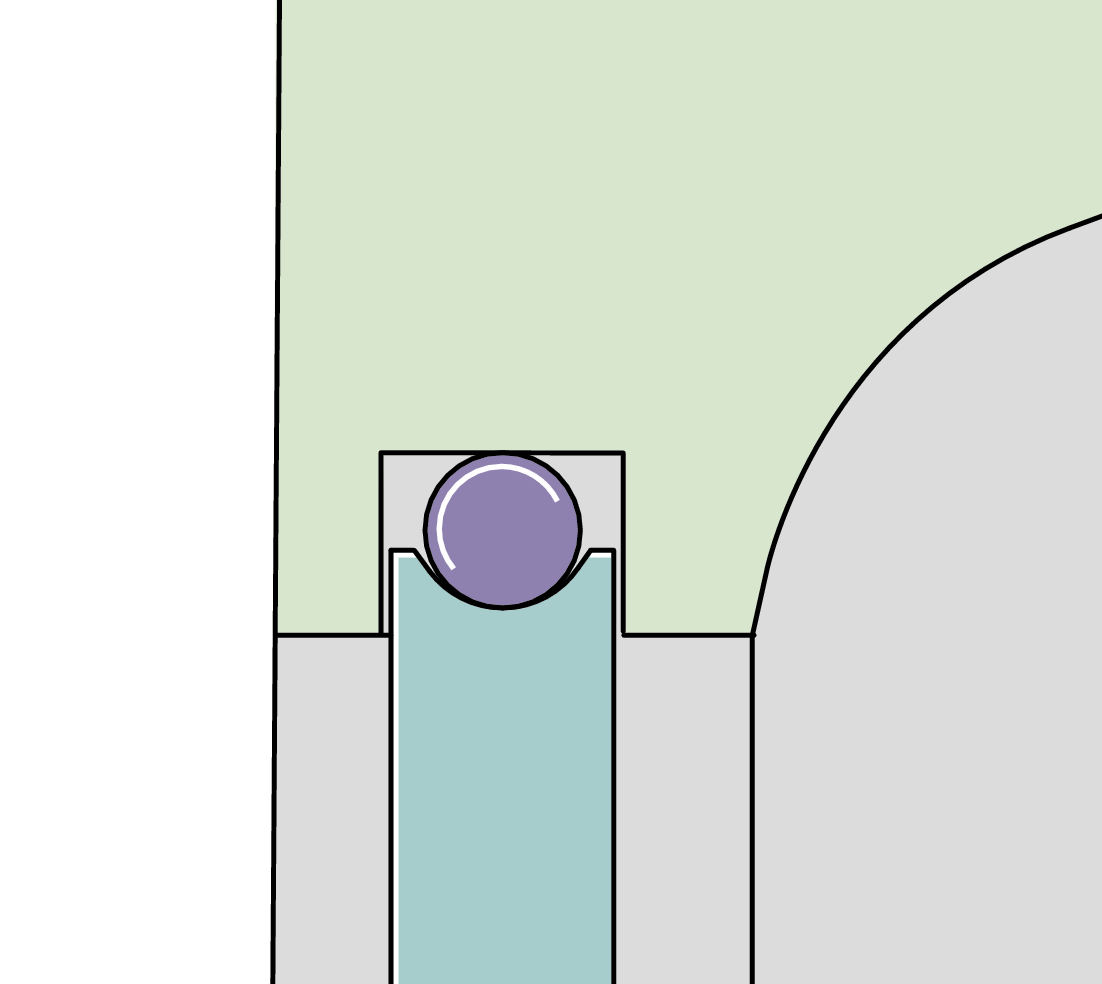 |
Designation
|
DH |
FSV |
TSV
|
Designation
|
DHV
|
TCV
|
DKV
|
DKVT
|
Material
|
NBR
|
Steel, felt, NBR
|
Steel, FKM
|
Material
|
Steel, NBR
|
Steel, NBR
|
Plastic
|
Steel or cast iron, FKM
|
Pieces per pack
|
2 |
2 |
1
|
Pieces per pack
|
1
|
1
|
1
|
1
|
Suitability for sealing against
|
|
Suitability for sealing against
|
|
dust
|
++
|
+
|
+
|
|
dust
|
+
|
++
|
+
|
+
|
fine, solid particles
|
++
|
–
|
+
|
fine, solid particles
|
+
|
++
|
+
|
+
|
coarse, solid particles
|
+
|
–
|
+
|
coarse, solid particles
|
–
|
++
|
+
|
+
|
slivers
|
+
|
+
|
++
|
slivers
|
–
|
++
|
+
|
+
|
spray liquids
|
+
|
–
|
–
|
spray liquids
|
+
|
++
|
+
|
+
|
Operating limits
|
|
Operating limits
|
|
Long term temperature
|
°C
|
–40 to +100 (due to NBR)
|
–30 to +100 (due to NBR)
|
–20 to +200 (due to FKM)
|
|
Long term temperature
|
°C
|
–30 to +100 (due to NBR)
|
–30 to +100 (due to NBR)
|
–40 to +120
|
–20 to +200 (due to FKM)
|
°F
|
–40 to +210 (due to NBR)
|
–22 to +210 (due to NBR)
|
–4 to +390 (due to FKM)
|
°F
|
–22 to +210 (due to NBR)
|
–22 to +210 (due to NBR)
|
–40 to +250
|
–4 to +390 (due to FKM)
|
Circumferential velocity
|
m/s
|
≦13 (continuous 6)
|
5 (after running-in 15)
|
No restriction
|
Circumferential velocity
|
m/s
|
≦12
|
≦12
|
Not applicable
|
Not applicable
|
Misalignment
|
°
|
≦0,5
|
≦0,5
|
≦0,5
|
Misalignment
|
°
|
≦0,5
|
≦0,5
|
Not applicable
|
Not applicable
|
Low friction
|
++
|
–
|
++
|
Low friction
|
++
|
+
|
Not applicable
|
Not applicable
|
Axial shaft displacement (suitability as non-locating bearing)
|
++
|
++
|
+
|
Axial shaft displacement (suitability as non-locating bearing)
|
(+)
|
+
|
Not applicable
|
Not applicable
|
Vertical arrangement
|
+
|
–
|
–
|
Vertical arrangement
|
(+)
|
–
|
+
|
+
|
Suitability for grease relubrication
|
++
|
–
|
+
|
Suitability for grease relubrication
|
(+)
|
+
|
+
|
++
|
Suitability for oil lubrication
|
(+)
|
–
|
–
|
Suitability for oil lubrication
|
–
|
–
|
–
|
++
|
Compatibility with sunlight
|
+
|
++
|
++
|
Compatibility with sunlight
|
–
|
++
|
(+)
|
++
|
Preconditions
|
|
Preconditions
|
|
Tolerance class1) of shaft diameter
|
h8 (h9)
|
h8 (h9)
|
h8 (h9)
|
|
Tolerance class1) of shaft diameter
|
h8 (h9)
|
h8 (h9)
|
Not applicable
|
Not applicable
|
Shaft roughness
|
μm
|
Ra 3,2
|
Ra 3,2
|
Ra 3,2
|
Shaft roughness
|
μm
|
Ra 3,2
|
Ra 3,2
|
Not applicable
|
Not applicable
|
- The envelope requirement Ⓔ applies.
Dimensions
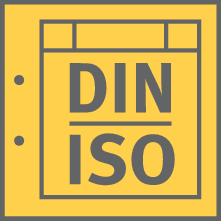
The dimensions of housings SNV correspond to ISO 113 and DIN 736 to DIN 739.
Interchangeability
The housings SNV are interchangeable with the existing housings SN and SNE.
Tolerances for the bearing seat
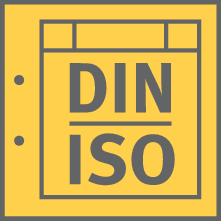
The bearing seat in split plummer block housings SNV is machined to the tolerance class G7 in accordance with DIN EN ISO 286-1. The tolerance indicated is valid in the delivered condition, i. e. before the screws connecting the upper and lower sections are loosened.
By agreement, the housings can also be supplied with other tolerance classes for the bearing seat.