Inhaltsverzeichnis
Vierpunktlager
- Lagerausführung
- Belastbarkeit
- Ausgleich von Winkelfehlern
- Schmierung
- Abdichtung
- Drehzahlen
- Geräusch
- Temperaturbereich
- Käfige
- Lagerluft
- Abmessungen, Toleranzen
- Nachsetzzeichen
- Aufbau der Lagerbezeichnung
- Dimensionierung
- Mindestbelastung
- Gestaltung der Lagerung
- Ein- und Ausbau
- Rechtshinweis zur Datenaktualität
- Weiterführende Informationen
Vierpunktlager
Vierpunktlager eignen sich gut, wenn:
- überwiegend axiale Belastungen aufgenommen werden müssen
- der axiale Bauraum für zweireihige Radial-Schrägkugellager nicht ausreicht
- radiale Kräfte von einem separaten Radiallager aufgenommen werden
- axiale Kräfte in beiden Richtungen auftreten und eine enge axiale Führung bei geringer Lagerbreite gefordert ist, z. B. im Getriebebau.
Vierpunktlager und zweireihiges Schrägkugellager – Bauraumvergleich B = Lagerbreite |
![]() |
Lagerausführung
Ausführungsvarianten
Vierpunktlager gibt es als:
- Lager der Grundausführung
- Lager mit Haltenuten im Außenring
- X-life-Lager
Lager der Grundausführung
Vom Produktdesign her vergleichbar mit einreihigen Radial-Schrägkugellagern
Vierpunktlager sind einreihige, nicht selbsthaltende Radial-Kugellager. Sie gleichen in ihrem Aufbau einreihigen Radial-Schrägkugellagern; die Laufbahnen in den Lagerringen sind jedoch so gestaltet, dass sie Axialbelastungen in beiden Richtungen aufnehmen können. Die Krümmungsmittelpunkte der kreisbogenförmigen Laufbahnen im Innen- und Außenring sind so gegeneinander versetzt, dass die Kugeln die Laufringe bei radialer Belastung in vier Punkten berühren.
Axial schmaler bauend als zweireihige Schrägkugellager
Diese Lager haben massive Außenringe, geteilte Innenringe und Kugelkränze mit Messing- oder Polyamidkäfig. Aufgrund des zweiteiligen Innenrings kann eine große Anzahl Kugeln im Lager untergebracht werden. Die Innenringhälften sind auf das jeweilige Lager abgestimmt und dürfen nicht mit denen gleich großer Lager vertauscht werden. In axialer Richtung bauen Vierpunktlager deutlich schmaler als beispielsweise zweireihige Schrägkugellager.
Vierpunktlager der Grundausführung α = Nenndruckwinkel M1, M2 = Krümmungsmittelpunkte der Außenringlaufbahn Fr = Radiale Belastung Fa = Axiale Belastung
|
![]() |
Lager mit Haltenuten im Außenring
Durch die Haltenuten kann das Lager einfach im Gehäuse festgelegt werden
Vierpunktlager werden häufig mit einem Radiallager kombiniert und als Axiallager mit radialem Spiel im Gehäuse eingesetzt. Zur schnellen und sicheren Festlegung der Lager im Gehäuse haben größere Lager deshalb zwei um 180° versetzte Haltenuten in einer Stirnseite des Außenrings. In diese Haltenuten greifen Sicherungsstifte ein, die den Außenring im Gehäuse festlegen.
Vierpunktlager als Axiallager eingesetzt, radiales Spiel am Außenring, axialer Kraftfluss
|
![]() |
X-life-Premiumqualität
Vierpunktlager gibt es in bestimmten Abmessungen als X-life-Lager. Gegenüber Standard-Vierpunktlagern sind diese Lager wesentlich leistungsstärker. Erreicht wird das u. a. durch die geänderte Innenkonstruktion und höhere Oberflächengüte der Kontaktflächen, das optimierte Käfigdesign sowie durch die bessere Qualität des Stahls und der Wälzkörper.
Vorteile
Höherer Kundennutzen durch X-life
Aus den technischen Detailverbesserungen ergeben sich eine Reihe von Vorteilen wie z. B.:
- eine günstigere Lastverteilung im Lager und damit eine höhere dynamische Belastbarkeit der Lager
- eine höhere Laufruhe
- ein reibungsärmerer, energieeffizienterer Lauf
- eine niedrigere Wärmeentwicklung im Lager
- höhere mögliche Drehzahlen
- ein geringerer Schmierstoffverbrauch und dadurch längere Wartungsintervalle
- eine messbar längere Gebrauchsdauer
- eine hohe Betriebssicherheit
- kompakt bauende, umweltfreundliche Lagerungen.
Niedrigere Betriebskosten, höhere Maschinenverfügbarkeit
In Summe verbessern diese Vorteile die Gesamtwirtschaftlichkeit der Lagerstelle deutlich und erhöhen damit die Effizienz der Maschine und Anlage nachhaltig.
Nachsetzzeichen XL
X-life-Vierpunktlager haben das Nachsetzzeichen XL im Kurzzeichen
Vergleich der dynamischen Tragzahl Cr – Lagerreihe QJ3..‑XL, Bohrungskennzahl 5 bis 14, mit einem Lager ohne X-life-Qualitäten Cr = Dynamische Tragzahl
|
![]() |
Anwendungsbereiche
Breites Einsatzspektrum
Aufgrund ihrer besonderen technischen Merkmale eignen sich X-life-Vierpunktlager sehr gut für Lagerungen in:
- Kompressoren
- Flüssigkeits- und Hydraulikpumpen
- Automotive-Fahrwerken und -Getrieben
- Industrie-, Eisenbahn- und Windradgetrieben
- landwirtschaftlichen Fahrzeugen und Geräten.
X-life steht für eine hohe Produkt-Leistungsdichte und damit für einen besonders großen Kundennutzen. Weitere Informationen zu X-life
Belastbarkeit
Axial beidseitig hoch belastbar
Durch die Gestaltung der Laufbahnen mit ihren hohen Schultern, dem großen Nenndruckwinkel von α0 = 35° und der hohen Anzahl von Wälzkörpern sind Vierpunktlager axial sehr tragfähig. Sie sind für wechselnde, rein axiale Belastungen oder überwiegende Axiallast geeignet. Dabei berühren die Kugeln den Innen- und Außenring nur in je einem Punkt wie bei einem axial belasteten einreihigen Schrägkugellager.
Die radiale Belastbarkeit der Lager ist gering. Bei überwiegend radialer Belastung sollen Vierpunktlager wegen der höheren Reibung im Vierpunktkontakt nicht eingesetzt werden.
Ausgleich von Winkelfehlern
Vierpunktlager können keine Fluchtungsfehler ausgleichen
Vierpunktlager eignen sich nicht zum Ausgleich von Fluchtungsfehlern bei Gehäuseverformungen oder Wellendurchbiegungen. Eine mögliche Schiefstellung des Innenrings gegenüber dem Außenring hängt u. a. von der Lagerbelastung, dem Betriebsspiel und der Lagergröße ab und ist sehr gering.
Schiefstellungen der Lagerringe erhöhen das Laufgeräusch, beanspruchen die Käfige stärker und wirken sich nachteilig auf die Gebrauchsdauer der Lager aus.
Schmierung
Öl- oder Fettschmierung
Die Lager sind nicht befettet. Sie müssen mit Öl oder Fett geschmiert werden.
Verträglichkeit mit Kunststoffkäfigen
Werden Lager mit Kunststoffkäfig verwendet, ist sicherzustellen, dass beim Einsatz von Syntheseölen oder Schmierfetten auf Syntheseölbasis sowie bei Schmierstoffen mit einem hohen Anteil an EP‑Zusätzen die Verträglichkeit des Schmierstoffs mit dem Käfigmaterial gegeben ist.
Ölwechselfristen einhalten
Gealtertes Öl und im Öl enthaltene Additive können bei höheren Temperaturen die Gebrauchsdauer der Kunststoffe beeinträchtigen. Vorgegebene Ölwechselfristen müssen deshalb unbedingt eingehalten werden.
Abdichtung
Die Lager sind offen
Vierpunktlager werden ohne Abdichtung geliefert. Die Abdichtung der Lagerstelle muss deshalb in der Anschlusskonstruktion erfolgen. Die Abdichtung muss zuverlässig verhindern, dass:
- Feuchtigkeit und Verunreinigungen in das Lager gelangen
- Schmierstoff aus dem Lager austritt.
Drehzahlen
Höhere Drehzahlen sind nur bei rein axialer Belastung möglich
Wegen des Vierpunktkontaktes und der damit verbundenen höheren Reibung ist die Drehzahleignung der Lager bei radialer Belastung stark begrenzt. Höhere Drehzahlen werden nur erreicht, wenn Vierpunktlager ausschließlich axial belastet werden.
Grenz- und Bezugsdrehzahlen in den Produkttabellen
In den Produkttabellen sind in der Regel zwei Drehzahlen angegeben
- die kinematische Grenzdrehzahl nG
- die thermische Bezugsdrehzahl nϑr.
Grenzdrehzahl
Die Grenzdrehzahl nG ist die kinematisch zulässige Drehzahl eines Lagers. Sie darf auch bei günstigen Einbau- und Betriebsbedingungen nicht ohne vorherige Rücksprache mit Schaeffler überschritten werden. Die Werte in den Produkttabellen gelten für Ölschmierung.
Werte bei Fettschmierung
Bei Fettschmierung sind jeweils 75% des in den Produkttabellen angegebenen Wertes zulässig.
Bezugsdrehzahlen
nϑr dient zur Berechnung von nϑ
Die thermische Bezugsdrehzahl nϑr ist keine anwendungsbezogene Drehzahlgrenze, sondern eine rechnerische Hilfsgröße zur Ermittlung der thermisch zulässigen Betriebsdrehzahl nϑ.
Geräusch
Als neues Merkmal zum Vergleich des Geräuschniveaus unterschiedlicher Lagerarten und Baureihen wurde der Schaeffler Geräuschindex (SGI) entwickelt. Damit ist es erstmals möglich, eine Geräuschbewertung von Wälzlagern durchzuführen.
Schaeffler Geräuschindex
Der SGI-Wert basiert auf dem nach internen Standards maximal zulässigen Geräuschniveau eines Lagers, welches in Anlehnung an ISO 15242 ermittelt wird. Zum Vergleich unterschiedlicher Lagerarten und Baureihen ist der SGI-Wert über der statischen Tragzahl C0 aufgetragen.
Damit ist es möglich, Lager gleicher Tragfähigkeit direkt zu vergleichen. In den Diagrammen ist jeweils der obere Grenzwert angegeben. Das bedeutet, dass das durchschnittliche Geräuschniveau der Lager noch kleiner ist, als im Diagramm dargestellt.
Der Schaeffler Geräuschindex ist ein zusätzliches Leistungsmerkmal zur Lagerauswahl bei geräuschsensiblen Anwendungen. Die spezifische Eignung eines Lagers für eine Anwendung, beispielsweise hinsichtlich Bauraum, Tragfähigkeit oder Drehzahlgrenze, ist davon unabhängig zu prüfen.
Schaeffler Geräuschindex für Vierpunktlager SGI = Schaeffler Geräuschindex C0 = Statische Tragzahl |
![]() |
Temperaturbereich
Limitierende Größen
Die Betriebstemperatur der Lager ist begrenzt durch:
- die Maßstabilität der Lagerringe und Wälzkörper
- den Käfig
- den Schmierstoff.
Mögliche Betriebstemperaturen der Vierpunktlager.
Zulässige Temperaturbereiche
Betriebstemperatur |
Vierpunktlager |
|
---|---|---|
mit Messingkäfig |
mit Polyamidkäfig PA66 |
|
|
–30 °C bis +150 °C, |
–30 °C bis +120 °C |
Sind Temperaturen zu erwarten, die außerhalb der angegebenen Werte liegen, bitte bei Schaeffler rückfragen.
Käfige
Standard sind Massivkäfige aus Messing und Polyamid PA66
Standardkäfige und zusätzliche Ausführungen für Vierpunktlager. Andere Käfigausführungen sind auf Anfrage lieferbar. Bei solchen Käfigen können jedoch die Eignung für hohe Drehzahlen und hohe Temperaturen sowie die Tragzahlen von den Angaben für die Lager mit den Standardkäfigen abweichen.
Bei hohen Dauertemperaturen und Anwendungen mit schwierigen Betriebsbedingungen sollten Lager mit Messing- oder Stahlblechkäfig eingesetzt werden. Bestehen Unsicherheiten bezüglich der Käfigeignung, bitte bei Schaeffler rückfragen.
Käfig, Käfignachsetzzeichen, Bohrungskennzahl
Lagerreihe |
Massivkäfig aus Messing |
Massivkäfig aus Polyamid PA66 |
||
---|---|---|---|---|
MPA |
TVP |
|||
Standard |
zusätzlich bei |
Standard |
zusätzlich bei |
|
Bohrungskennzahl |
||||
QJ10 |
12, 17, 19, 21, 22, 24, 26, 30 bis 40 |
‒ |
‒ |
‒ |
QJ2 |
bis 08, 10, 13, 16, 17, ab 19 |
09, 11, 12, 14, 15, 18 |
09, 11,12, 14, 15, 18 |
08 |
QJ3 |
03, 04, ab 10 |
05 bis 09 |
05 bis 09 |
‒ |
Lagerluft
Axiale Lagerluft
Standard ist CN
Vierpunktlager werden serienmäßig mit der axialen Lagerluft CN (normal) gefertigt. CN wird im Kurzzeichen nicht angegeben.
Darüber hinaus sind bestimmte Abmessungen auf Anfrage auch mit der kleineren Lagerluft C2 sowie mit der größeren Lagerluft C3 und C4 lieferbar.
Die Werte der axialen Lagerluft entsprechen DIN 628-4:2008 (ISO 5753‑2:2010). Sie gelten für Lager im unbelasteten, messkraftfreien Zustand (ohne elastische Deformation).
Axiale Lagerluft von Vierpunktlagern
Nenndurchmesser der Bohrung |
Axiale Lagerluft |
||||||||
---|---|---|---|---|---|---|---|---|---|
d mm |
C2 μm |
CN μm |
C3 μm |
C4 μm |
|||||
über |
bis |
min. |
max. |
min. |
max. |
min. |
max. |
min. |
max. |
10 |
18 |
15 |
65 |
50 |
95 |
85 |
130 |
120 |
165 |
18 |
40 |
25 |
75 |
65 |
110 |
100 |
150 |
135 |
185 |
40 |
60 |
35 |
85 |
75 |
125 |
110 |
165 |
150 |
200 |
60 |
80 |
45 |
100 |
85 |
140 |
125 |
175 |
165 |
215 |
80 |
100 |
55 |
110 |
95 |
150 |
135 |
190 |
180 |
235 |
100 |
140 |
70 |
130 |
115 |
175 |
160 |
220 |
205 |
265 |
140 |
180 |
90 |
155 |
135 |
200 |
185 |
250 |
235 |
300 |
180 |
220 |
105 |
175 |
155 |
225 |
210 |
280 |
260 |
330 |
Abmessungen, Toleranzen
Abmessungsnormen
Die Hauptabmessungen der Vierpunktlager entsprechen DIN 628‑4:2008. Nennmaße der Vierpunktlager.
Kantenabstände
Die Grenzmaße für Kantenabstände entsprechen DIN 620‑6:2004. Übersicht und Grenzwerte. Nennmaß des Kantenabstands.
Toleranzen
Die Toleranzen für die Maß- und Laufgenauigkeit der Vierpunktlager entsprechen der Toleranzklasse Normal nach ISO 492:2014. Toleranzwerte nach ISO 492.
Haltenuten
Die Abmessungen und Toleranzen der Haltenuten entsprechen ISO 20515:2012 bzw. DIN 628-4:2008.
Nachsetzzeichen
Die Bedeutung der in diesem Kapitel verwendeten Nachsetzzeichen zeigt, sowie medias interchange http://www.schaeffler.de/std/1B69.
Nachsetzzeichen und ihre Bedeutung
Nachsetzzeichen |
Bedeutung der Nachsetzzeichen |
|
---|---|---|
C2 |
Axialluft C2 (kleiner als normal) |
Sonderausführung, |
C3 |
Axialluft C3 (größer als normal) |
|
C4 |
Axialluft C4 (größer als C3) |
|
MPA |
Massivkäfig aus Messing, |
Standard, Käfigwerkstoff abhängig von der Lagerreihe und der Bohrungskennzahl |
TVP |
Massivkäfig aus glasfaserverstärktem Polyamid PA66 |
|
XL |
X-life-Lager |
Standard, abhängig von der Bohrungskennzahl |
N2 |
zwei Haltenuten im Außenring |
Standard bei |
Aufbau der Lagerbezeichnung
Beispiel zur Bildung der Lagerbezeichnung
Die Bezeichnung der Lager folgt einem festgelegten Schema. Ein Beispiel dazu zeigt. Für die Bildung der Kurzzeichen gilt DIN 623-1.
Vierpunktlager mit zwei Haltenuten im Außenring: Aufbau des Kurzzeichens |
![]() |
Dimensionierung
Dynamische äquivalente Lagerbelastung
P = Fr bei rein radialer Belastung konstanter Größe und Richtung
Die zur Dimensionierung dynamisch beanspruchter Lager verwendete Lebensdauer-Grundgleichung L = (Cr/P)p setzt eine Belastung konstanter Größe und Richtung voraus. Bei Radiallagern ist das eine rein radiale Belastung Fr. Ist dies gegeben, wird in die Lebensdauergleichung für P die Lagerbelastung Fr eingesetzt (P = Fr).
P ist eine Ersatzkraft bei kombinierter Belastung und bei verschiedenen Lastfällen
Trifft diese Bedingung nicht zu, muss zur Lebensdauerberechnung zunächst eine konstante Radialkraft bestimmt werden, die (was die Lebensdauer betrifft) eine gleichwertige Beanspruchung darstellt. Diese Kraft wird dynamische äquivalente Lagerbelastung P genannt.
Fa/Fr ≦ 0,95 oder Fa/Fr > 0,95
Die Berechnung von P hängt vom Belastungsverhältnis Fa/Fr und dem Faktor 0,95 ab.
Dynamische äquivalente Belastung

Dynamische äquivalente Belastung

Legende
P | N |
Dynamische äquivalente Lagerbelastung |
Fr | N |
Radiale Belastung |
Fa | N |
Axiale Belastung. |
Statische äquivalente Lagerbelastung
Für statisch beanspruchte Vierpunktlager gilt.
Statische äquivalente Belastung

Legende
P0 | N |
Statische äquivalente Lagerbelastung |
F0r, F0a | N |
Größte auftretende radiale oder axiale Belastung (Maximalbelastung). |
Statische Tragsicherheit
S0 = C0/P0
Neben der nominellen Lebensdauer L (L10h) ist immer auch die statische Tragsicherheit S0 zu überprüfen.
Statische Tragsicherheit
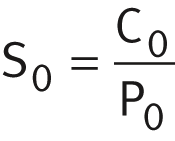
Legende
S0 |
Statische Tragsicherheit |
|
C0 | N |
Statische Tragzahl |
P0 | N |
Statische äquivalente Lagerbelastung. |
Mindestbelastung
Um Schlupfschäden zu vermeiden, ist eine axiale Mindestbelastung von Fa ≧ 1,2 · Fr notwendig
Für eine niedrige Reibung im Lager ist, besonders bei hohen Drehzahlen, eine axiale Mindestbelastung erforderlich. Damit die Reibung im Lager nicht zu sehr ansteigt, soll die Axialkraft so hoch sein, dass die Wälzkörper die Innen- und Außenringlaufbahn jeweils nur in einem Punkt berühren. Das ist gegeben, wenn Fa ≧ 1,2 · Fr ist.
Gestaltung der Lagerung
Einsatz als Axiallager
Ist ein Vierpunktlager als reines Axiallager vorgesehen, muss der Außenring im Gehäuse radiales Spiel haben, um das Lager radial nicht zu belasten.
Lagerringe auf ganzem Umfang und ganzer Breite abstützen
Damit die Tragfähigkeit der Lager voll genutzt werden kann und so auch die geforderte Lebensdauer erreicht wird, müssen die Lagerringe durch Auflageflächen auf ihrem ganzen Umfang und über die volle Laufbahnbreite fest und gleichmäßig abgestützt werden (gilt nicht für Lager mit radial freigestelltem Außenring). Die Sitz- und Auflageflächen sollen nicht durch Nuten, Bohrungen oder sonstige Ausnehmungen unterbrochen sein. Die Genauigkeit der Gegenstücke muss bestimmten Anforderungen entsprechen.
Radiale Befestigung der Lager – Passungsempfehlungen
Für eine sichere radiale Befestigung sind feste Passungen notwendig
Neben der ausreichenden Abstützung der Ringe müssen die Lager auch radial sicher befestigt werden, damit die Lagerringe auf den Gegenstücken unter Last nicht wandern. Das geschieht im Allgemeinen durch feste Passungen zwischen den Lagerringen und den Gegenstücken. Werden die Ringe nicht ausreichend oder fehlerhaft befestigt, kann dies zu schweren Schäden an den Lagern und angrenzenden Maschinenteilen führen. Bei der Wahl der Passungen sind Einflussgrößen wie Umlaufverhältnisse, die Höhe der Belastung, die Lagerluft, Temperaturverhältnisse, die Ausführung der Gegenstücke und Ein- und Ausbaumöglichkeiten zu berücksichtigen.
Treten stoßartige Belastungen auf, sind feste Passungen (Übergangs- oder Übermaßpassung) notwendig, damit sich die Ringe zu keinem Zeitpunkt lockern. Zu Spiel-, Übergangs- oder Übermaßpassung.
Bei der Gestaltung der Lagerung sind die folgenden Angaben aus den technischen Grundlagen zu berücksichtigen:
- Umlaufverhältnisse
- Toleranzklassen für zylindrische Wellensitze (Radiallager)
- Wellenpassungen
- Toleranzklassen für Lagersitze in Gehäusen (Radiallager)
- Gehäusepassungen.
Festlegung des Außenrings durch Haltenuten
Zur Festsetzung der Lager im Gehäuse mittels Haltenuten und Sicherungsstift.
Axiale Befestigung der Lager – Befestigungsarten
Die Lager müssen auch in axialer Richtung sicher festgelegt sein
Da eine feste Passung allein meist nicht ausreicht, die Lagerringe auf der Welle und in der Gehäusebohrung auch in axialer Richtung sicher festzulegen, muss dies in der Regel durch eine zusätzliche axiale Befestigung bzw. Sicherung erfolgen. Die axiale Fixierung der Lagerringe ist auf die Art der Lageranordnung abzustimmen. Geeignet sind prinzipiell Wellen- und Gehäuseschultern, Gehäusedeckel, Muttern, Abstandsringe, Sicherungsringe usw.
Maß-, Form- und Laufgenauigkeit für die Lagersitze
Für den Wellensitz mindestens IT6, für den Gehäusesitz mindestens IT7 vorsehen
Die Genauigkeit des Lagersitzes auf der Welle und im Gehäuse soll der Genauigkeit des eingesetzten Lagers entsprechen. Bei Vierpunktlagern mit der Toleranzklasse Normal soll der Wellensitz mindestens dem Grundtoleranzgrad IT6, der Gehäusesitz mindestens IT7 entsprechen. Richtwerte für die Form- und Lagetoleranzen der Lagersitzflächen, Toleranzen t1 bis t3 entsprechend. Zahlenwerte für die IT-Qualitäten.
Richtwerte für die Form- und Lagetoleranzen der Lagersitzflächen
Toleranzklasse |
Lagersitzfläche |
Grundtoleranzgrade nach ISO 286-1 |
||||
---|---|---|---|---|---|---|
nach ISO 492 |
nach DIN 620 |
Durchmessertoleranz |
Rundheits-toleranz |
Parallelitätstoleranz |
Gesamtplanlauf-toleranz |
|
t1 |
t2 |
t3 |
||||
Normal |
PN (P0) |
Welle |
IT6 (IT5) |
Umfangslast |
Umfangslast |
IT4 |
Punktlast |
Punktlast |
|||||
Gehäuse |
IT7 (IT6) |
Umfangslast |
Umfangslast |
IT5 |
||
Punktlast |
Punktlast |
Zahlenwerte für ISO-Grundtoleranzen (IT-Qualitäten) nach ISO 286-1:2010
IT-Qualität |
Nennmaß in mm |
||||||||
---|---|---|---|---|---|---|---|---|---|
über |
10 |
18 |
30 |
50 |
80 |
120 |
180 |
250 |
|
bis |
18 |
30 |
50 |
80 |
120 |
180 |
250 |
315 |
|
Werte in μm |
|||||||||
IT4 |
5 |
6 |
7 |
8 |
10 |
12 |
14 |
16 |
|
IT5 |
8 |
9 |
11 |
13 |
15 |
18 |
20 |
23 |
|
IT6 |
11 |
13 |
16 |
19 |
22 |
25 |
29 |
32 |
|
IT7 |
18 |
21 |
25 |
30 |
35 |
40 |
46 |
52 |
Rauheit zylindrischer Lagersitzflächen
Ra darf nicht zu groß sein
Die Rauheit der Lagersitze ist auf die Toleranzklasse der Lager abzustimmen. Der Mittenrauwert Ra darf nicht zu groß werden, damit der Übermaßverlust in Grenzen bleibt. Die Wellen müssen geschliffen, die Bohrungen feingedreht werden. Richtwerte in Abhängigkeit von der IT‑Qualität der Lagersitzflächen ➤ Tabelle.
Rauheitswerte für zylindrische Lagersitzflächen – Richtwerte
Nenndurchmesser d (D) |
empfohlener Mittenrauwert |
||||
---|---|---|---|---|---|
mm |
μm |
||||
Durchmessertoleranz (IT-Qualität) |
|||||
über |
bis |
IT7 |
IT6 |
IT5 |
IT4 |
‒ |
80 |
1,6 |
0,8 |
0,4 |
0,2 |
80 |
500 |
1,6 |
1,6 |
0,8 |
0,4 |
Anschlussmaße für die Anlageflächen der Lagerringe
Die Anlageflächen für die Ringe müssen ausreichend hoch sein
Die Anschlussmaße von Wellen- und Gehäuseschultern, Abstandsringen usw. müssen sicherstellen, dass die Anlageflächen für die Lagerringe ausreichend hoch sind. Sie müssen jedoch auch zuverlässig verhindern, dass umlaufende Teile des Lagers an feststehenden Teilen anstreifen. Bewährte Anschlussmaße für die Radien und die Durchmesser der Anlageschultern ➤ Maßtabelle. Diese Maße sind Grenzmaße (Größt- oder Kleinstmaße); sie dürfen nicht über- oder unterschritten werden.
Ein- und Ausbau
Die Ein- und Ausbaumöglichkeiten der Vierpunktlager mit thermischen, hydraulischen oder mechanischen Verfahren sind bereits bei der Gestaltung der Lagerstelle zu berücksichtigen.
Die Lager sind montagefreundlich, da nicht selbsthaltend
Vierpunktlager sind nicht selbsthaltend. Dadurch lassen sich der Außenring mit dem Kugelkranz und die beiden Innenringhälften getrennt voneinander einbauen➤ Abschnitt. Das vereinfacht den Einbau der Lager.
Schaeffler-Montagehandbuch
Wälzlager sehr sorgfältig behandeln
Wälzlager sind vielfach bewährte Präzisions-Maschinenelemente zur Gestaltung wirtschaftlicher, zuverlässiger und betriebssicherer Lagerungen. Damit diese Produkte ihre Funktion einwandfrei erfüllen und die vorgesehene Gebrauchsdauer ohne Beeinträchtigung erreichen, müssen sie sorgfältig behandelt werden.
Das Schaeffler-Montagehandbuch MH 1 informiert umfassend über die sachgemäße Lagerung, Montage, Demontage und Wartung rotatorischer Wälzlager http://www.schaeffler.de/std/1B68. Daneben enthält es Angaben, die der Konstrukteur für den Ein‑ und Ausbau und die Wartung der Lager schon bei der Gestaltung der Lagerstelle beachten muss. Das Buch liefert Schaeffler auf Anfrage.
Rechtshinweis zur Datenaktualität
Die Weiterentwicklung der Produkte kann auch zu technischen Änderungen an Katalogprodukten führen
Im Mittelpunkt des Interesses von Schaeffler stehen die Optimierung und die Weiterentwicklung seiner Produkte und die Zufriedenheit seiner Kunden. Damit Sie sich als Kunde bestmöglich über diesen Fortschritt und den aktuellen technischen Stand der Produkte informieren können, veröffentlichen wir Produktänderungen gegenüber der gedruckten Ausgabe in unserem elektronischen Produktkatalog.
Änderungen der Angaben und Darstellungen dieses Katalogs behalten wir uns daher vor. Dieser Katalog gibt den Stand bei Drucklegung wieder. Neuere Veröffentlichungen unsererseits (in Printmedien oder digital) gehen automatisch diesem Katalog vor, soweit sie dasselbe Thema betreffen. Bitte prüfen Sie daher stets über unseren elektronischen Produktkatalog, ob aktuellere Informationen oder Änderungshinweise für Ihr gewünschtes Produkt verfügbar sind.
Weiterführende Informationen
Bei der Auslegung einer Lagerung sind neben den Angaben in diesem Kapitel auch folgende Kapitel in den technischen Grundlagen zu beachten: